СДЕЛАЛИ ГОНЧАРНЫЙ КРУГ, НО ЧТО-ТО ПОШЛО НЕ ТАК
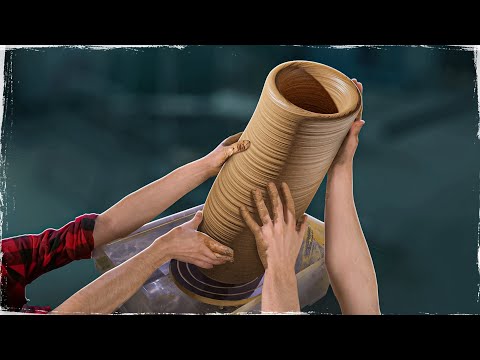
hello to you, danya craster, and today we will try ourselves in the role of potters, we made a self-made potter's wheel and smear ourselves in clay to the fullest, in short, I will cross out once we try to plunge into the technology in which you don’t take a foot in a tooth at all for one, is it as simple as it seems, well, we round it up to visit the master in order to understand our mistakes and show how to do it right , no matter what anyone says, but each business has its own entry threshold and we need a minimum set of tools and materials to start looking at the prices of pottery wheels, we were a little crazy and immediately decided to collect we ourselves have a hair of a treadmill from one of the past vids all over its little pilot I’m so a bit of a Bulgarian unwell, finally it’s not like thieves to look for a new one so that it’s inexpensive exactly Alice where a battery grinder is cheaper, the choice of big prices is different everywhere, so we turned to the fox who quickly sorted everything out and helped to find the best option, our new Bulgarian points are already on the way, but for now we will squeeze out all the juices from the old one, so we cut the pipe approximately in half and start the operation of transplanting the bearing. the potter's wheel is a rather simple thing, but even here there are troubles if we simplify the design, this is a basin in which an axis is mounted in the center on which the metal potter's wheel rotates, the axis must be rigid and even circle in no case should it dangle and fidget, while all this we construct should easily rotate naturally on bearings, and here clay with water comes into play, which, by any means, tries to crap all moving nodes in the very first minutes of work, shorter tasks and looks simple and only at first glance, but we ’ll come up with housing to treat today, we again do everything without drawings and with minimal calculations what we will get in the end and for there is only from the remnants of common sense in our heads, actually when we talked about that zik, we’re here in general they never joked if you look at the photo of the potter's wheels, it's worth sleeping there and on the one that is lying around grandmas in the country, we will go in a more budgetary way and use a plastic container and in order to attach to it we made a plate of metal and on top we sew a piece of plywood at the corners of the plate and we make 4 holes in the center we pronounce a triangular hole with old Soviet blunt cheese and beauty so that guilt does not fall in the bearing and did not replace the lubricant , we decided to install an oil seal for the oil seal, you need a ring into which it will be inserted, here is such a set of parts, we got at this stage a pair to connect it together so as not to overheat the bearing, we put the pipe literally tormentors of the point, there are rumors that one point can withstand 80 kilograms so it will go well, and after everything is stuck together, and we swing the basement hole from the tube, pulled it into such a detail, the fault is both a limiter and a seal for the stuffing box, one problem is a tube of too large diameter, we take a piece of thin tin and push it into the pipe, the solution is not the most correct engineer, but but the fastest and now the solution from the never series so don’t put the ring for the stuffing box, stick the stuffing box inside and the shaft align everything in place, the ring is a little larger in diameter than necessary, so the stuffing box enters it almost effortlessly now we grabbed all this welding in place and quickly pull out the stuffing box until it melts and then avaline the ring in a circle welding will tighten the ring and the seal will sit there as it should the seal we have a very complicated relationship with chain drives on the one hand we use them all the time and they allow some inaccuracy in manufacturing and on the other they send us the fuck in every project this case is no exception in the bins they dug up some kind of rusty piece of iron that perfectly fit under the asterisk of course the piece of iron and the basement did not fit, so we muddy the adapter from a piece of pipe and collect everything to the heap, we can say we are at the finish line, at least I spent most of the time in this project with us it was on the chain drive and the shaft that he always wanted to assemble from shit and sticks and in the process completely kept to this concept, it turns out it’s not so scary yet they haven’t forgotten the asterisk, it is placed last because on its sharp edges there will be an important mission to fix the shaft of the rotary mechanism, of course, we don’t even think that the device needs to be serviced and lubricated , so we will strengthen everything on the old one good smarka and all the backlash and diligently remove by putting pieces of tin in our channel about garage technologies and lydia we don’t make a rocket in the end, of course, everything superfluous would be amputated from the ridge, the steel on it is not horseradish, understand what is sawn with difficulty, maybe from the rest we’ll try something then even forge it, but now we are going to the grinder for the time that we have this home-made master grinder, we have already thought many times about how to redo some nodes, but this guy still won’t break, well, it’s like something and it turns out now we need to think about how to turn all this in our bins is a motor with a gearbox on which we didn’t do anything this dude in he helped us out many times when we needed to rotate something slowly with sufficient force, but this time we clearly don’t have enough speed, so we assemble the overdrive chain from the star from the front crank of the bicycle and it remains to figure out how to attach this star here among the scrap metal we found this here’s a pancake that fits perfectly in diameter no, it’s not we who were so lucky we didn’t prepare behind the scenes, just during the work of the master we will hide and overgrown with scraps and unused blanks, and during a recent forced move we collected all this in one pile and among this scrap metal now you can find at least the devil the only thing left for the bald man is to drag the almost finished part to our needs and in some cases remove the age-old rust so that by this year it can be somehow welded moving to a small workshop there is one plus all the machines and we always connect all this nearby [ __ ] and try to align percussion star in a way, all welded to one point and precise tuning ku can be carried out with the help of a thickness gauge rod and a hammer, then we scald and think about how to fix it all on the motor now direct it, it’s the mount, it ’s the tension system, we have already used such a video design how to get a neighbor and we liked this method of attachment, I’ll mark by the way here you say that we we do a lot of things and then where do we keep a secret just saw pieces of a square pipe at first it was a bicycle polisher then we made a stand for airbags and now a profile pipe has found its last refuge in a potter's wheel well, or not the last hell knows how it will go further we take a bicycle there are cyclists in the team, so from time to time we have old new spare parts, the chain is no exception here everything is standard, you are the first half of the war, we connect the required length as we lie down and assemble it, and the brother design works, but there is a nuance due to the fact that everyone cooked at random the transformation of the cycle it stretches then weakens in these cases smart d the perfectionists are redoing everything anew, but we’ll simplify our task and now we’ll build some kind of clamp, we’ve been lying around lonely and the wheels are infernal with dead bearings, but we won’t let it die just like that, let it suffer even more, we weld all this canoe to the frame tensioner and tighten the roller with a spring it should turn out to be eco and a kind of wheel to calm down, which will pull up the sagging workshop in those moments when it tries to sag, it will not allow the chain to run away and in general it worked according to engineering, well, what kind of potter's wheel without the wheel itself is also not just a circle and from hell , understand what if everything to do spiders, it must be made of metal on the disk, they make annular grooves so that the transformations and processing of clay do not strive to jump to the side, only 1 pro will work for us. we make the rest more like decorative and as a material we took, although good, but still laminated plywood is not the best choice, but the easiest to process, besides, it copes well with humidity, we used and when we made a modular workbench, the transformer vidos is also on the channel check it out if you haven't seen it yet, but only after this video, whoever watches each of our releases will find a bunch of kisses from the past vidos, for example, silhouettes are visible on this plywood . which is what the grooves did on both sides, we mill the plywood half the depth and get the perfect circle just what we need as a basin and decided to use this plastic container here we just do everything in the center of the force hole with the world and set the container aside until better times before everything assemble, think about connecting a plywood pancake and a metal shaft, we didn’t come up with anything for me m to climb our heap of scrap metal and find something suitable there, well, almost suitable, we had a piece of iron gis lying around with a randomly obtained special conical hole, of course, the shaft also needs to be sharpened plus or minus on a cone and in a quick way this can be done with a grinding disc for the unit turned on behind the scenes from plywood they made a small base on which the nut motor will hold, by the way, also with a history of they used airbags, a video about which was literally a couple of months ago so that the mixture of clay and water does not pour onto the motor, everything that can be smeared with liquid nails , yes, these are liquid nails, they are sealant and the final chord in the frame is a plywood overlay , it will sew the whole structure even more tightly into a single one, it will be an excellent basis for which we will fasten the container, but at this moment we directly felt what happens when you win in a hurry, let's make sense 3 self-tapping screws spun normally one brain for all of us and fucked good we remembered about the special stray that we are for torelli especially for such purposes, if at the stage of welding the part was slightly turned, such inconveniences would not be again generously coated with everything if they are glued together on the glue screws so that water does not pour out through the cracks and its potter, but if you compare this 100 croak dublin this hand blank is a chisel and water is sosh you work without soot to the forest the end you work we fold our hands to the forest also the end of the new one times slower we thought for a long time how to fasten the metal blank to plywood but it was already approaching night and it became more difficult to think so we welded a nut in a circle and with self-tapping screws on wood we screwed a small square , taking into account the accuracy when processing literally everything in this project, we still have to set the ball to a large one, wrapped it with masking tape so that in which case we could remove the circle, but in the end we left the idea as a simple plywood circle, we will screw the square onto a self-tapping screw through a layer of dense rubber by tightening the screws, it will be possible to set the level of the plywood circle and get rid of the beating Surprisingly, the design received and rigid adequate and it is quite possible to use it , only clay is left to be found, but Zhanna turned out that modern evening and use ready-made mixtures and find dry clay in the form of a powder organ cup is much more difficult and more expensive than the finished mixture, nevertheless, the mixture needs to be kneaded and stick it in the center of the circle and there you will find it, in general, we were the wildest glad that the topic of potters is more alive than all living things and there are many shops with consumables and many books from where you can get knowledge, but knowledge is one thing and experience ebs arshin is another , we see a potter's wheel in the first time and you won’t believe how difficult it is to do something exactly , giving a spanking to try to align the workpiece that stubbornly leads to the side to work with metal or wood is not at all like if you think that you will pick up a potter’s wheel and start riveting smooth jugs like a factory break off we decided to make a small coffee service, a jug for milk, a sugar bowl and a glass, and it seems that something even turned out, but the most important thing is ahead of us - firing , we left the dishes for several days to dry completely, while this product can be slightly modified with a knife to cut off excess influxes, but you can’t stick the kiln in this form, first you need to judge the oven at 200 degrees so that bound water comes out of the clay and only after that you can put the blanks into the kiln for firing, our forge is not quite suitable for such purposes, but the firing goes on at temperatures of more than a thousand degrees, and our helgi die already at five hundred shorter, put it in the forge and we’ll see if it turns out it won’t work out how the card will fall earlier in general, they burned on the fires and nothing burned the product needs to be cooled along with the forge, but the broken piece has already been introduced , let's wait a bit and see what we got, everything has cooled down and now it is clear that the firing went to a strong deuce, it seems that it was baked in the sugar bowl, it became many times stronger, but cracks appeared and in in those places where the fire fell, the clay became a gray special house did not work out, so it's time for us to call to a master who will explain to us how to fire correctly and generally tell us how the grill works , here we are, and in the present ceramics studio, the hostess who conducts master classes, we are lucky and she will conduct today's master class especially for you. modeling from clay, all the shelves are filled with her works and the works of students, and now we will see what operations need to be carried out with clay and in order for it to turn from a nondescript mass into a work of art, everything starts with clay, a piece is kneaded on a towel so that the mixture becomes more homogeneous, this process takes seconds in the frame in reality, the clay is kneaded much longer, the prepared mixture kneads the cake, specifically this mass contains fireclay fireclay, this is fired and crushed clay, and by adding the mixture they make the mass for modeling more unpretentious in drying and firing, and the finished product will turn out stronger , that is, the mass on the table consists of raw clay fired clay and the water obtained shines, it is necessary to roll out so that the walls of the future product are of the same thickness , now the tool is entering, although for the simplest basic form you only need a knife, they cut off the torn edges, which can crack when baked, then the edges of the resulting workpiece are smoothed again, we asked to do something simple and the most a simple form for hand-sculpting and this is a plate while the forms have not yet dried on it, you can print what we will not have with us except for self-tapping screws or a key, there was nothing and I will tell you these things and obviously they were not created for that, but let's see what comes of it now the form is sent to dry, the process is long, so we asked to show all the stages on the already dried products, these are white clay products and now they are gray, this is exactly until the moment they go into the oven, this is the heart of the pottery workshop and this heart works for days, for example, only one the original appearance lasts all day the burnt blank of the century cools and tears with glaze if you simplify glaze it is glass dust with a pigment diluted in water and if you have not worked with glaze you will never guess what color it is until you burn the product now you see a slightly greenish solution but after firing it will become beige glaze is diluted with water to the state of thick cream and applied to the already burned workpiece with a brush, excess moisture is absorbed into the shard and a layer of glass powder forms on the surface during baking, the glass melts and covers the entire product, protecting it from moisture and smoothing out irregularities there are matte glazes there are glossy there is pigment and which are applied to the glaze or under it, the game is shorter; zooming in on this is almost a separate science; the only rule is that they don’t apply to the lower part; otherwise, when baking in the oven, the products will stick tightly; you can take a ceramic plate or mug and look at its bottom; you will see that the point of contact with the table is not covered by anything ; bake and re-bake the whole de the whole point is that a controller is connected to the oven that controls the temperature and does not allow it to rise too quickly so that the workpiece has time to dry and does not burst, and just as slowly cools naturally, I don’t put one product into the oven and try to load it to the maximum, do it in two For the first reason, no one wants to wait a day for the sake of firing one mug, and the second such oven lives electricity like damned electricity bills fly to heaven and this is how white clay looks at different stages from left to right drying firing and glazing after drying the clay is gray and loose after the first firing particles of clay sinter products turn white and become much harder and the last stage of glazing the glaze smoothes the shape and makes it absolutely impervious to moisture and easy to use. this is such a journey into the world of pottery, we got it, we hope you were interested as well as us subscribe to the channel ставьте лайк и пишите в комментах какие ремесла вам было бы интересно увидеть в следующих роликах ну а мы отправляемся работать дальше чтобы почаще радовать вас крутыми видосами с вами был даня крастер мастерская build not bombs пока
2022-05-01 07:57