ONE THING AFTER ANOTHER
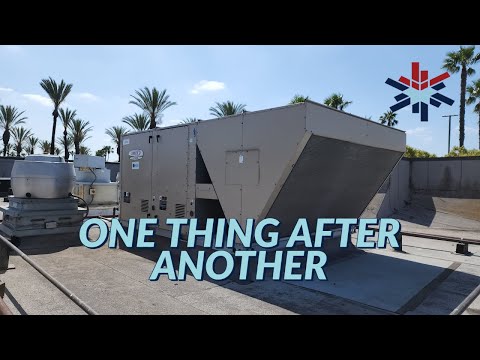
so I pulled the condenser fan motor thing right here and I just wanted to see motor's not hot it came unplugged the little plug wasn't making a good connection so it might have been an intermittent problem that's interesting huh I'll have to put some zip ties on that make that a more permanent strap this video is brought to you by sporland quality integrity and tradition today I'm called on a kitchen AC that's this guy right here and they're saying that it's not working now we had a service call about a week ago and sent some service technicians out here they said the kitchen was hot and this customer does not do routine maintenance so I sent a couple guys out here to do PM service and uh just clean the units up check everything out and the customer was fine after that but I knew I still had to come back out so I left the work order open so I'm back here today to kind of get my eyes on everything so first and foremost this is our kitchen AC the thermostat settings are all out of whack it's a mess okay management does has it doesn't have a clue as to what's going on they just know it's hot when I got here this morning all the thermostats were set to off not in program mode and I'm like why did why are they turned off and the manager was like well because it was cold in here so I turned all the thermostats off and it's like no that's not how it works you don't turn them off you turn them off right so this is what we're dealing with we're having to battle people that don't understand and it's not the manager's fault they're not trained properly on how the HVAC system works and this is a a problem with the restaurants right now because they can't you know it's all new staff and everything so anyways first thing I do is I turn on the exhaust fans whenever you're dealing with a kitchen problem you always check the exhaust fans okay so I come over and I can feel all the air moving out of the exhaust fans but I noticed that this one's not moving very much air right and the belt is extremely loose like it's barely even doing anything okay so don't just look at the thermostat don't just look at the AC look at the building as a system okay the building is a complete system all of it and if the exhaust isn't working it's going to lead to high heat in the kitchen okay so first I'm going to do is I'm going to go through here and adjust all these belts make sure they're nice and tight I got all the belts tightened up everything's good on those now the AC I walk up to the unit and first thing I notice is that it says fresh air Cooling and the discharge air temp is 96 degrees the discharge air temp is not 96 degrees fresh air cooling is a feature that we have to temper the ducts okay and if the ductwork temperatures get above a certain threshold the air conditioning turns on and if it gets below a certain threshold the the heating turns on regardless of the demand from the thermostat okay now this guy shouldn't be sane 96 degrees discharge air temperature more than likely we've got a bad discharge air temp sensor which is right here okay so we need to look into that but but for now what that'll do is uh the manager was complaining that it was freezing in the kitchen this morning so she turned off the air conditioner well that's likely because of the fresh air Cooling so what we need to do is power down the unit and then we're going to uh actually not power down the unit we actually need to go in and disable Fresh Air Heating and Cooling until we can get that discharge air temperature replaced so we're going to do is go into setup test and balance damper we're gonna have to go through this set point select let's save that Supply Air set point okay that's for uh economizing now we're going to go through here so is damper closed we need to go make sure that the damper is closed and then once we go through the calibration of the damper then we'll be able to turn the fresh air cooling and heating on and off so we got to wait for this guy to close all the way once it's closed all the way then we'll um we'll go through the steps okay the damper is closed so we're going to go ahead and answer yes and we gotta wait for it to open now [Music] all right the damper is completely open now so at this point we can go ahead and answer that question and then it's going to lead us to the to the question about fresh air cooling and heating so we change it to Yes uh we've got our minimum and maximum uh damper settings blower on high lower on low I'm gonna leave those alone we don't want any ventilation options and I'm going to disable Fresh Air Heating and disable fresh air cooling okay so now we've disabled that okay problem solved now we need to figure out um if there's anything else going on with the unit or if it's just a programming issue all right this is odd so we have an occupied signal oh because someone has R and ocp jumped out that's not correct typically we want the occupied signal to come from the G terminal so that way when the thermostat is calling for um yeah I'm gonna change that over to the G but we don't have a demand right now that is odd we should have an indoor fan running 24 7 right now and we don't um well the indoor fan should run whenever the building is occupied for Air Balance reasons here all right I'm going through the uh settings right now and we have some interesting errors in here alarm value economizing when it shouldn't uh okay drain pan overflow five seven I believe my technicians that were here when they came they they told me the drain pan was plugged up so they that's an inch um freeze stat open Alarm 34 this was five six drain pan compressor two free stat economizing when it shouldn't so that's interesting we need to look into that um okay so I don't think I need to go too much further than those errors right there I'm going to go ahead and clear the alarm history um I don't really care too much more and we're gonna go ahead and uh proceed so we need to look into why it was economizing when it shouldn't and then we know about the drain pan issue oh the freeze stats too um my guys did not put a new belt on this unit I believe they put a new belt on another unit so free stats could have been caused by loose belts so we need to probe up on these guys to check the pressures to figure out possibly if it's a refrigeration issue causing a free stat but it's interesting because now the blower is on I all I I did switch it over to the Occupy to the G so here's the theory behind that the occupied mode this unit's economizer and outside air dampers will open to the minimum position when the the unit is occupied because we need the outside air dampers open to bring in fresh air into the building but you don't want that to happen when nobody's in the building you only want it to happen when it's occupied so the reason why I have occupied hooked up to G is because the way we run these thermostats whenever they are in the building the indoor fan runs now we don't have humidity here in Southern California it's very minimal so that's why we do it that way I realize in humid climates you may not want to run the indoor blower all the time you can balance your building different ways in humid climates but here this is how we typically do it so I switched that over but it's interesting though that the blower wasn't running a few minutes ago and now it is running you can tell a lot just from observing so it just went to no demand and the fan turned off again so I definitely need to go down to the thermostat and see what's going on there's something funky in the thermostat that's causing a problem that's intermittently turning power on and off coming up to the unit it doesn't hurt just to step back and watch for a few minutes I've been up here for 10 15 minutes just just watching the unit operate and I'm noticing that the indoor fan is turning on and off erratically really so come up here and uh this is our bar this should be our kitchen and this should be the dining room this one right here should be the one that's our problem it says occupied there should be no reason why this thing's it's actually set for 69. so it should be cooling at the moment let's look at our fan settings fan is on and it's not sending power up to the unit everything looks good there I don't know what is going on here I wonder why this is doing this look at the thermostat sensor too apparently they decided uh duct tape would hold it together so we'll have to fix that in order to prove that the thermostat this is the one that I needed I jumped R to G and I can feel the fan turn on I've got a register right above my head so I know that this is the kitchen AC there was nothing wrong with the connection on the thermostat it was on there nice and tight so that's going to lead me to believe that we have a bad thermostat so we're going to go ahead and replace the thermostat and put a new Zone sensor and then see where that gets us all right got a new Honeywell stat installed just need to program it and then we'll go up and see if we get any more of that intermittent issues anymore and I'm also going to install a new Zone sensor so all right we are set up and all probed up I have the large pipe clamps the jl3lc which go from three quarter all the way up to four and an eighth inch pipe size so these are great for large pipe for heavy industrial Light commercial like I do they work out in certain situations too so we're all set up on the job link app we just got to put this unit into test mode so we're going to go Service Test cool and go down to three select and all the compressors should start turning on and we're going to let the system stabilize out and run for a bit and then we'll test the um data and see what it says so using field piece and their temperature clamps you have the regular clamps okay and then you have the large ones okay the lock they both use the rapid rail technology so you have to make sure that you clean the pipe notice that it's a little shiny right there because it uses that pipe to get its temperature reading so it has to be clean okay these things you can take them off and when you open them they lose connection you put them back on and they'll make the connection again so and also they were designed in the way that if the pipe isn't too dirty you can literally scrape it back and forth and it's okay to do that and that'll help to clean it too so this system is just about stabilized out you can see that I'm testing three compressors at the same time that's why I got my S man out I actually have enough probes to do three compressors but I don't have enough probes to get discharge pressure at the same time so I'm getting liquid pressure and discharge pressure so I can see the differential between the two so coming up here using the job link app now you can get a delivered capacity right here now the delivered capacity you do have to measure the airflow now I put 6 000 because that's what this unit requires but I actually didn't measure the airflow I'd say a conservative number would probably be 5500 would be a safe number to assume so once we input that and we hit done we'll get a capacity change right there not too much but a little bit okay so you actually have to measure the airflow you can use a hot wire anemometer you can you know get in there and figure it out that way if you want now I also have a vfd driven system but uh this one right here is on when all three compressors are running that vfd runs at full speed okay so I think our delivered capacity is within range again I didn't actually measure it I'm just making an assumption um air side we're about a 20 degree temperature split uh compressor number one we have about eight degrees super heat 12 degrees sub cooling notice that there's a 30-something PSI difference from liquid to discharge pressure that is normal okay about the same on compressor number two about a 30 PSI pressure difference 11 degrees sub cooling 8 degrees super heat this guy's running a little bit higher on the subcoin 14 degrees 13 degrees it's kind of moving around and about 12 degrees super heat so I'm not seeing any real issues with this system refrigerant wise remember that we had uh freeze stat safeties meaning that the evaporator got too cold well we look at our saturation temperature for compressor number one is about 40 degrees compressor number 236 compressor number 336 I'm not seeing any problem in that so I think that maybe when my technicians were out here the first time maybe they tightened up that belt maybe they had a loose belt before they did that okay so this unit I changed the thermostat everything seems to be working proper on it um I I really don't see any other issues other than we need to get a new discharge air temperature sensor because it's reading 93 degrees when it's not 93 degrees um everything else checks out okay so don't see any other issues with the unit condenser is clean condenser fan motors are staging because it's only 75 degrees outside so this condenser fan motor is not running yet [Music] um coming over here everything's looking good metal mesh filters are clean don't see any issues there air filters are clean they use a filter changing company to change those so I don't see any issues with those this unit's checking out so I think we're going to call it with a new thermostat and uh tell them to keep an eye on it and then we'll definitely talk to them about changing that discharge air temperature sensor all right we are back today I've got the discharge air sensor for this but customer said they're still having issues so let's open this up interesting okay y1 Y2 ocpg with no demand we have no Demand on this right now well I shouldn't say that it's not running but we have a code 30 and a code 147 147 is not a big deal but code 30 is something but look at that we're calling for y1 and Y2 but we're not turning on so the last time my guys were here they were cleaning the unit up for me they noticed that they had a drain pan overflow switch issue and they cleaned the drain pen because it was plugged up but look at that alarm code 30 drain pan overflow switch so yeah this unit's trying to run but the Overflow switch is locking it out so I need to find that overflow switch figure out if I can even get one today how to bypass it what's going on with it but we can look over here and make sure that drain pads dry I know it's hard for you guys to see that but yeah it's bone dry so we're good there this is my switch right here these two wires so I imagine we either make or break a circuit here so we could probably bypass it by jumping these two out possibly or removing one of these weird all of a sudden now we're actually getting an alarm popping up so okay um alarming value drain pen overflow shutdown so it's shut down on drain pan overflow so I need to do some research and find out if I need to make or break that circuit so that's interesting um when I went to go pull the connector apart it broke off in my hands so maybe it's just a loose connection I'm currently running a new discharge air temperature sensor and look at that we go off on high pressure on compressor number three that's interesting I wonder if we got a fan motor what is what the heck man why now we check pressures and everything all right well we'll get to that too so I pulled the condenser fan motor thing right here and I just wanted to see motor's not hot it came unplugged the little plug wasn't making a good connection so it might have been an intermittent problem that's interesting huh I'll have to put some zip ties on that make that a more permanent strap all right I zip tied up that connector so that way this makes a super tight connection all the condenser fan motors are running I went ahead and installed a new discharge air temperature sensor I rerouted it to the other section over there so this is it right here um also went through and uh because we get an error code 147 on here right and 147 is a motorized outside air damper not working properly I went through and actually changed the configuration because this unit was set up for an outdoor enthalpy sensor for the economizer I changed that to minimum outside air damper because that's how we operate these buildings is with minimum outside air it's like a corporate thing so we set it up for minimum outside air I changed the unit so it no longer is an economizer it literally just opens 20 or 30 percent dependent on the blower speed and uh so that 147 really is irrelevant I honestly don't even know why I'm getting that code because in order to set the dampers position I had to modulate the dampers and they work fine so maybe it's not getting feedback back to the board or something but honestly I'm not going to investigate that problem anymore so I'm going to watch this unit for a little bit longer it's really weird how we were getting these intermittent problems right because I was here the other day and I think I saw the hit in the history of the Overflow switch but it wasn't active when I was here and my company or my guys had just cleared that sweat or the drain because it was plugged up I didn't see anything about high pressure but I saw freeze stats and that's why I put my gauges on it and checked everything everything looked fine we had a little bit higher than normal sub cooling on the third stage but at the time I don't think all the condenser fan motors were running so I really didn't see a need to jump into that any further just because I didn't see any high pressure codes in the board but you know in true fashion it ended up being something with the condenser fan motor although I'll have to review the footage maybe you guys remember I thought this fan motor was running I thought those ones weren't but regardless they're all running now everything's good the unit's operational [Music] discharge air sensors good we're just going to keep an eye on it I'm gonna watch it for another 20 25 minutes make sure we don't get any other errors and start cleaning up my messes I swear this take right now is like the fourth take I've done trying to do this outro because my animals keep coming to my door my cats are meowing my dog is whining I let the dog in the office I started over he starts whining again in the middle of recording this I'm gonna pull my freaking beard hairs out I'm going crazy trying to record the outro to this video these are some serious first world problems right all right let's get on with the outro okay so I want to address uh the preventative maintenance that I said I sent my technicians out to do first and foremost understand that um I did not send my guys out to look at the whole building now I know I I said you know when you're doing equipment when you're working on kitchen ACS you want to look at the whole building understand something these videos that I make are for my technicians the whole point of me starting this YouTube channel um initially wasn't supposed to be a public channel it's just the way that I troubleshoot and instead of taking my guys with me and paying them to watch and follow me all day long um I make the videos and I just say hey watch these when you get a chance okay so and I realize that there's educational value that comes to other people whether you like my troubleshooting you may get educational value because you're like I'm never going to do it the way that he does it because it's wrong who knows okay but regardless the whole point is to learn from these videos whether it be something that I did correct or something that I did incorrect okay so with that being said when I sent my guys out here I literally sent them out to just clean the ACs we have a lot of customers that don't do any routine maintenance and so when we go out to do a service call it's no longer a two-hour service call because you got to clean the equipment before you can even diagnose the equipment so you end up spending six to seven hours on one piece of equipment and it's annoying right so usually what I do to save myself time is I'll send some people out hey just go clean the equipment triage it for me and then I'll come in and I'll troubleshoot right especially when I know it's going to be a complicated issue which unfortunately just tends to be more and more complicated stuff this one was a one thing after another service call it just seemed that everything kept coming it can be very easy to get lost in these one thing after another calls and also it can be very easy for the customer to get frustrated and upset with you because especially if you know you you you don't have the ability to troubleshoot multiple things and there's nothing wrong with that because everybody has different service levels or levels uh skill levels I should say you know that which they can diagnose things and I'm not perfect I'm sure there's people much better than I okay um so this was a confusing one and you know remember that when your customers start complaining well you just fix it or you just cleaned it well you know what if you don't maintain your equipment regularly little problems can escalate to this kind of stuff okay um so it is what it is just do your best and and remember that it's okay to step back and watch I get so many YouTube comments I wish I had this much time to spend on a service call if you're being pushed through your service calls now I understand In The Heat Of Summer sometimes you got to do what you got to do you know you're super busy but remember that when you're on a job site you need to be on that job site that's the way that I treat my customers when I'm there I'm there okay I'm not already thinking of the next call I'm focusing on this call now I understand that you get super busy and sometimes I'll say I'll go through my crazy mode where I just got to put fires out and move on to the next one when we get big heat waves sometimes I'm just literally going around resetting high pressure controls rinsing off condensers and then coming back later to evaluate all the equipment okay that sometimes has to happen but I don't think it's acceptable for a company to expect someone to handle 10 service calls especially on Commercial 10 service calls in a day you're not giving the customer any value if you can't spend time at their equipment now I also understand the flip side that you know if customers don't maintain their equipment it's hard to to have someone park at a job site to clean and then evaluate you know so it's kind of a fine balance and it's you know whatever but for the people that leave in my comments I wish I had this much time I I think you need to start evaluating um you know where you work if if you're not being given the proper time to be able to diagnose and evaluate equipment now you know it's completely understandable you know that again when you get busy you have to do what you have to do but I don't know I don't know where I'm going with that but just remember the people that are in my comments always saying like I don't know how you have that much time you know I don't know how they don't have that much time like you know I mean there's something going on there so we need to give the customer the proper time okay um you know I I see issues with all sides of that but regardless we got out there I sent some guys out to kind of quickly clean the equipment I didn't expect them to go through everything okay um I came out first thing I did was evaluate the exhaust fence just from experience it's like dude let's let's knock this out heat comes from not being extracted from the building right cooking appliances and different things so let's get the exhaust system up and running tighten all the belts got that pulling all the air out of the building okay then I go to the kitchen AC and I start looking at it I notice that there's intermittent connection problems I noticed that there's a overflow switch problem I ended up disconnecting the over overflow switch completely that's out of the picture it's not going to trip in hindsight as I'm editing the video I started realizing you know what I probably could have disconnected that overflow switch by changing the unit configuration just like I did with the economizer I turned the economizer off set it for a minimum outside air position all you got to do is go into the unit setup and the Overflow switch honestly probably was in the configuration ID and I probably didn't have to just unplug it I probably could have just changed the configuration ID for the board so that way it doesn't even recognize the Overflow switch but I didn't do it that way you know whatever there's multiple ways to do things okay so overflow switch is out of the picture just seemed redundant talked to the customer they were okay with it because they don't do maintenance so you know and the design of the unit doesn't really allow like even if the drain pan overflows the way that Linux designed this unit for the return air there's actually a little like one inch lip at the the bottom of the unit before water goes into that so it actually just comes out the door before it drops down into the ductwork so I don't really think we're going to have an issue with that again customer needs to do routine maintenance right and they don't so it is what it is so overflow switch is out of the picture the thermostat went ahead and changed the thermostat because it was intermittently making a connection right there's nothing wrong with the the connection going between the thermostat and uh the AC on the flip side you guys didn't see it in this video a couple weeks later I got another service call for the AC and they were pissed they're like you just spent all this money again you know they're mad because they're like you spend all this money fixing this AC and it's broken again and it's like Well yeah if you maintain your damn equipment it we wouldn't run into these weird problems where you have tons of stuff wrong right but what ended up being wrong the time that you didn't see in this video was they busted that zone sensor again the one that had duct tape on it that I replaced they busted it again and it was just like guys it's because what they store the pans that they store right there the cooks just beat the crap out of that thing so we ended up putting a protective cover over the Zone sensor I tried to move it but it was long story it was difficult to move the Zone sensor but you didn't see that in this because that was a couple weeks after this video so back to I changed the thermostat got that going but then we started seeing other problems that's when I saw the Overflow switch okay so eliminated the Overflow switch uh saw the freeze stats so that's why I probed up on the system and went through the operations didn't see anything wrong with the refrigerant pressures compressors all seem to be fine everything seemed to be in line right but then I saw the high pressure switch and it's like wow why and that was the return visit right the high pressure switch went ahead and found that the condenser fan motor had come loose interesting right so zip tied that up so that way that wouldn't happen again and in the midst of that too I changed that discharge air sensor so that way it wouldn't be um you know going into or it wouldn't be giving them the false readings with the discharge air sensor so again I'm I I I'm pretty familiar with the Linux unit so maybe this was a little bit easier for me than it was for other people I'm sure that there's people that work on train units all day long that could diagnose them much faster than I can I happen to work on a lot of Linux units so I noticed the the weird intricacies that they have and I noticed the weird quirks that they have and you know I can kind of work my way through them but it's important when you're doing your troubleshooting just to fall back to the basics understand we're just moving heat that's all we're doing as as hvacr service technicians we are moving heat from one place to another okay if it's too cold in the building we're moving heat from the outside to the inside if it's you know and vice versa okay so we're just moving heat well I guess we're not moving heat from the outside of the inside we're tempering the air and heating it up or we're displacing the heat moving it from the inside to the outside is what we're doing really if it's a heat pump we're moving it from the outside to the inside but if it's a gas heat like this one then we're simply just taking the inside air and heating it up I'm going off on a tangent as I usually do I know that my brain works a little different than probably I'd expect other people's I'd probably screwed up in many ways there's probably a lot of undiagnosed stuff but I still appreciate the people that actually watch these videos and make it to the end it's awesome leave me a comment if you did make it to the end it's really cool to see how many people actually do you know thank you thank you to everybody this kind of you know gives me something to do uh you know this is kind of my hobby lately I'm trying to change a few things I have all kinds of ideas because I am getting a little like uh board I guess I can say with the the consistent same videos all the time like I'm getting a little weird so I've got some ideas on ways that I can change the channel I don't really want to change everything but you know um it's been five years I think I think so so 20 November of 2017 so 18 19 20 21 yeah we're going on five years this November that I've been making these YouTube videos it's kind of crazy so I need a little bit of change in there because it's like same bat Channel same bat time every day in my head you know sometimes I have to like I don't want to make another video um just because I the process that I have to go through but I've been trying to change a few things up make it kind of fun if you guys have ideas I'm always open to feedback feel free to send me an email hvacrvideos gmail.com you can leave it in the YouTube comments um just because you have an idea though I'm going to tell you right now uh if I don't like the idea I'm not going to do it okay even if there's an overwhelming amount of people that want me to do it because I do this channel the way that I want it to because I don't want it to be something that I'm not having fun with okay so it has to be something that I'm interested in um or I just it just becomes a job you know but hopefully someone gets something from this and I know I'm extremely rambling right now so I'm gonna stop that if you guys want to support the channel there's a couple different ways you can do so you can support the channel via Paypal patreon YouTube channel memberships those are monthly commitments that you make charges your credit card a fixed amount whatever you choose to do sends it to me they take their cut sends it to me and helps me to compensate for some of the time that I spend on this uh you can also you know during live streams and and even in the comments you can support it via super chat or super thanks I think on YouTube um there's my website hvacrvideos.com I have merchandise available on there the number one seller is this hat right here everybody loves these things they're a cool design I purposely designed them for service technicians they have a black underbill they're breathable so it's hard to tell but you can actually see through the Hat it's not a trucker hat it's it's really hard to explain but it's a really interesting design they're very breathable I sweat a lot less in these hats than I used to in other hats so they're really cool I purposely didn't put my logo on these hats because I didn't want to interfere with anybody's uniform policies again I'm a business owner so I think about that kind of stuff so I put the hvacr acronym on there with my color scheme that way potentially people can wear them with their normal uniforms and again not violate policies right so there's a lot that went into these so if you're interested check it out on my website we try to keep the prices as low as possible I'm not trying to make a fortune off a merchandise I think I make like five dollars a hat or something like that so it's not even that much sometimes you know I include shipping in the price so it's really not even that much if you're interested check it out there's shirts on there sweatshirts on there beanies on there um you know check it out also if you're interested in purchasing any tools go to truetechtools.com they're an affiliate that I work with they're a cool company I know a lot of the people there met him several times very cool people have they have a great selection of tools and we actually set up an affiliate program where if you use my offer code big picture one word uh I get or you get an eight percent discount I get a small commission from that um and uh yeah they just have a great selection of hvacr tools so check out truetechtools.com it's a great way to
help support the channel remember that I try to go live on YouTube Monday evenings about 5 p.m Pacific uh I know this upcoming week it is July 9th right now so this video will be released on July 10th and then July 11th I actually will not be doing a live stream because it's my daughter's birthday so be spending time with her on that one uh crazy thing is my daughter's 16th birthday is that not freaking Bonkers like dang man 16 year old daughter huh wow that's just crazy it's awesome though a lot of fun but it's just crazy that that time has gone by 16 years since I had my first kid wow and I know a lot of you guys have children much older than that so or guys and gals right have children much older than that but it's just crazy for me it's awesome I try to spend as much time with my family as possible thank you to all of you that support this channel by watching these videos um commenting and all that different stuff because you help me to be able to spend more time with my family so it's awesome okay so thank you so very much from the bottom of my heart my family's heart it's awesome again I really appreciate you but anyways uh live streams Monday evenings 5 p.m Pacific and then also Friday evenings I go live with my friends on the HVAC overtime YouTube channel about 605 PM Pacific usually a different style of show so be cautious uh it's a very uncensored show so if you get your feeling hurt by bad words and uh um weird topics you probably don't want to go to the show but if you have an open mind and just want to hang out like a bunch of guys at the bar come check out the HVAC overtime show for Friday evening 605 PM Pacific okay again I really appreciate you all and we will catch you on the next one okay
2022-07-12 20:35