Above and Beyond, Innovations in Aerospace AM
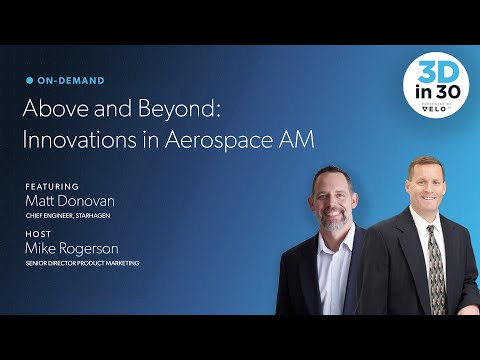
foreign [Music] welcome to the next episode of 3D in 30. uh today we're going to be talking about above and beyond the Innovations in Aerospace in am or additive manufacturing if you're not familiar with what AM refers to on this episode of 3 and 30 we're going to welcome an industry Dyno or as we refer to them an industry dinosaur this is Matt Donovan chief engineer at starhagen if you don't know what a dinosaur is a dinosaur is or a dino is an award they give at amug and it's for leaders in an industry industry people who have contributed a lot to the am industry and we're going to find out a little bit more about that later on in the show um you know Matt has a long history in the AM community and that's part of why he has the dino award uh looking at the transformation of this industry over the last 20 years and so that I always find this fascinating this is a technology that advelo 3D evolves weekly um we can do things a month from now that we can't do things today and this is kind of a common thing um and and for the whole industry it's been evolving very quickly so seeing that transition is pretty awesome uh we're also going to dive into Matt's career progression look at some of the challenges in his early days see where he thinks the future of the industry is going um we're going to look at starhagen that's his company where he is currently and look at some of their successes in Aerospace and defense so uh with no further Ado I'll bring Matt on and also as a reminder to our audience this is a live show we'd love to hear from you and uh we will get to your questions as quickly as we can there can be a delay between when you submit a question and when we see it so please allow for that and also sometimes if we're in just a really riveting conversation uh we do get sucked into that so just give us time um so Matt uh welcome to the show can you tell us a little bit about your background hi Mike thanks a lot appreciate the invite um my background is primarily I would say mostly in Aerospace I've been working in Aerospace since 1998 um started a small company that was making fuel injectors for jet engines and hot section components for that and I still consider myself a manufacturing engineer at heart but I've um you know we've kind of Twisted that position quite a bit as over the years as we've evolved a bunch of Technologies and uh so I worked in standard manufacturing for well until about 2006 and then I transferred into our research lab and at that time it was uh company was Goodrich and I started doing the advanced manufacturing and we were challenged with inventing new new technologies and new solutions to you know manufacturing problems for really making Advanced fuel injectors and hot section components for jet engines and that's when I was introduced introduced to a metal additive manufacturing back when I was working with uh Greg Morris and his team at Morris Technologies we had some really great successes early on and I'm very proud of the work that we did we invented a whole slew of different types of Innovations for fuel injectors as well as for the additive industry and I stayed there until 2017 and for a couple years I was at a company called erlicon doing the same thing uh helping customers build parts and then I went to jabal and got my some experience doing medical Parts as well as Aerospace components um so in addition to parts that we were making for the Apache helicopter one of our other facilities we were making spinal cages and knee Replacements so um got to work on a lot of very fun fields and then I stepped away from jabel and about a year or so ago just under a year ago I started here at starhagen and I'm meeting well all the additive effort here at starhagen so um when I started um August of the last year we just had an empty room and I think we'll show a picture in a little bit of what that room looks like now um I was really proud one of the things I was um for me what I feel was a really significant accomplishment was two months to the day of after I started and as I said it was a completely empty room when I started here we in we installed our Velo system and we actually shipped our first uh three parts for a second stage rocket engine within two months so that was so some that might not sound like a lot but for me it was really it was a great accomplishment I feel so that and you're kind of highlighting how quickly that turnaround time was what what have you experienced in the past for like you get a you get a system it shows up on your floor how long might it take in in previous roles to be shipping for Revenue um you know what I've generally told people if they're getting into it from the get-go starting from scratch I I tell them plan on nothing for the first year realistically I think you can it can be done faster depending on what who you bring on for talent what you have for funding and resources and there is an awful lot of facilities and infrastructure work that has to be done there's a lot of material development that has to be done for Aerospace um so it's an extensive body at work that there's a whole lot of things that most people just don't understand or see the behind the scenes all the dirty work that you have to do to get to a point to where you're ready to make parts and I I didn't just put it together like a second ago but the the companies that you mentioned previously um while they're all sort of innovators in high-tech comedy they're like erliken the first time I encountered them was in solar but then I found out how much business they did in Fabrics or making machines for Fabrics I I think it is G obviously does a ton of different things um you mentioned jabel they make just anything for anyone uh and additive in each of those cases probably not the primary revenue I think I wouldn't go out on a limb saying it's not the primary revenue contributor for any of those companies but now you're in starhagen where um now how would you see am fitting into starhagen's business model um you know at first blush um a lot of people probably wouldn't see a connection there um so before I started here at starhagen um we traditionally just manufactured components for aircraft Interiors so pretty much every part that uh you see on an aircraft uh seat bench you know the the fold out trays the struts yeah so that's a great example of an assembly that's up we make everything there but the seats and the seat belts themselves um so all the connectors all the the arms the hinges the take the trays including the the plastic parts we do vacuum forming plastic here as well so we make all of that here uh start again now that we're getting into additive we're you know really trying to step up our game um really get into you know the much more challenging you know air the the harder parts of Aerospace of you know the hot section the Exotic Metals um so I mean mostly the so so far the parts that we've made here in the 11 months that I've been here we've made a number of rocket engine parts helicopter gearboxes heat exchangers um missile fins and uh some other things I can't talk about now yeah we mentioned before Aerospace and defense not a very well-known industry for being open and transparent with what they're making um but it those are very different components like you look at uh you know these the seats kind of traditional business and now you're getting into hot sections uh obviously functional components engine components well have you seen a difference in delivering those parts to to customers are there are there different uh people that you're talking to um how would you describe kind of the business relationship with those um it's definitely a different working relationship um working with these Aerospace you know the big aerospace companies or the rocket companies and what have you versus our I would say our Legacy customer base you know for the conventional you know just milled tubes and uh struts and arms and uh you know drink trays and things like that they're frankly they're radically different animals um they deal in different quantities um and frankly one of the things that um one of the challenges that I'm working with our shop to bring online is most added the parts are completely different than conventional manufactured parts and a lot of that has to be worked through with so we've got a good machine shop out here we've got you know we're fully five axis as 9100 qualified machine shop and we have some very talented machinists and but if you haven't encountered the additive parts it's you have to kind of change your way of thinking of how am I going to make this part how am I going to machine it because frankly a lot of the parts that are designed aren't designed to be able to be machined um but you know uh the nice thing about working here we're small very lean organization and I work very closely with our subtractive Machining leads and every build that comes that comes up everything we quote we talk in depth about how do we want to build this how am I going to hold on to it what tooling are we going to need um it's it's just a completely different mindset that um most people are not prepared for so one of the my questions and you're probably the right person to ask this is am uh for a while it has maybe been the the smaller contributor in terms of Metal Manufacturing and a lot of the parts that people see in the real world are marketing samples they're parts that don't necessarily go through a lot of these post-processing steps um and it have you seen that Engineers are thinking about the post-processing in their approaches thinking about fixturing thinking about hold on to the part or is that something that you're Consulting with them on to kind of bring them up to speed I would say much more the matter um frankly and metal am is very challenging um and most people don't understand the the back end infrastructure that you need like you're talking about the post-processing so what heat treatment stress relieving hipping that's hot ice hot isostatic pressing um and edms electrical discharge Machining to separate parts from the build plates you need furnaces you need edms you need people with metal energy experience you need welding experience um actually I've given a couple talks at um you know trade shows like rapid and um and Fabtech actually talking people out of the metal am because you know machine shops um frankly they they see the uh Factor they see these really cool parts and frankly sometimes maybe some sales reps might be giving painting a Rosier picture of how easy it is um then you know then it really is um you know well frankly what I what I tell people when I was given these talks you know when people ask you know how much is this really going to cost what do I really need because they just see the machine cost they don't see all the other infrastructure and frankly what I tell people is take the cost of the machine that you're planning on buying and multiply that by five and that's probably the amount of investment you're going to need to get fully self-supported to get fully operational and qualified with test bars and metallurgical data and staff that you need to hire and inspection equipment it it's it's a pretty steep learning curve and it's not very forgiving yeah I I I've got one more observation and I just kind of want to bounce it off you and then we'll go to some questions here we've got a question from romsey that looks pretty good um I in in our past Velo 3D like if you look at additive Parts you see a lot of brackets you see uh topologically optimized General design whatever you want to say brackets and when we went through all of our sales processes um we didn't find a lot of value in in making brackets we found kind of what you're mentioning injectors rocket engines uh shot of impellers turbine components like the these are they're hot something a fluid is flowing through this part and the fluid flow that goes through that part is critical to the operation of the whole uh a whole assembly those are Parts where we feel like we've got a line of sight into and and I I don't think that am is is closely tied to that type of part um as I would expect but again I'm seeing a lot of the marketing things so what what is your thought on that or are we marketing this in the right way and getting out the right kind of Parts um so yes and no frankly um so you know people talk about brackets but you know um when I was working on some brackets for a customer you know Airbus had over a thousand brackets of a certain type that they use on one of their planes and um very common when I was working in the hot section areas uh pounds cost dollars so you know everything you can do to shave weight off of a part yeah even if a bracket might be a little bit more expensive if you can shave a significant amount of weight over it you know when you've got a thousand of those on a plane that adds up to a lot of fuel savings so um you know yes there's some really fancy brackets out there and you know GE had a design Challenge on that a couple years back that was really fun um and I'm seeing literally hundreds of different types of brackets um but it you know it depends on what the the need of the customer is you know like in Aerospace weight means more than any weight in performance usually mean more than costs um where I see a whole lot of uh opportunities frankly is going to be casting Replacements as we get these bigger machines that can do you know aluminum castings uh you know actually part I'm working on right now um for an aerospace customer is investigating can I make um a comparable quality uh to a legacy casting that they've got and I feel very confident that we'll be able to do that and make it in fact much better but it's not just the the casting side of it it's this the lead time you know so when you know when you're developing these new uh next-gen uh air dominance Fighters for example there's going to be a lot of complex parts you can't wait 18 months to two years to get your first part you need them now so and then you know additive permits us to make Parts very fast we get you know um a lot of people have heard the Mantra get to fail faster so you can iterate and learn quickly um and change your designs and that was one of the early areas that uh we saw opportunity in when I was at previous places but um I see it even more and more every day now we do have a question from uh romsey I hope I'm getting your name right do we need to change or update the PLM steps is generative design and out of manufacturing are already changing the common product development process what are your thoughts on that so I'm assuming we're referring to a product life cycle management is PLM so um there are there are a lot of PLM challenges frankly um for me PLM systems you know you can make it work with additive but it is every place that I've worked at has had different challenges with their PLM systems both managing the models and um the design configurations um over the years you know it's really easy to fall into a trap of making the wrong configuration of a part and you just you know threw away maybe thirty thousand dollars um by making the wrong configuration if you don't have good pln control but also um you know on the Erp side as well a lot of these systems like sap JD Edwards job boss whatever um they really struggle with how to how to incorporate um this completely different way of managing things you know because they're used to you know buying certified bar stock and I just okay I need six inches for this part and we just cut off a chunk and off you go um you know create a traveler and what have you versus is here I'm taking a metal plate and I'm taking some powder and voila here's a part and they're like well how do I manage that yeah that's interesting I also think when you decide on your manufacturing solution depending on how your company has done PLM in the past Could Happen very early um versus pushing for optimization and then looking for a manufacturing solution we've done a number of case studies with customers where the order in which you do that can open the door to additive or it can shut the door for additive and it's kind of interesting I've seen a lot of parts that you know people well frankly they get sticker shock when they think they've got a great part for additive but you know frankly if you're making a high volume casting and you don't have supply chain problems it's probably not going to be cost competitive if it's a little 30 widget that you can cast by the thousands now if it's a big housing that you know you have high high mix and low volume uh it probably is a good uh opportunity I would say you know when I was in working on fuel injectors there is a number of great opportunities for particularly the land-based engines when we as we're learning and building our qualifications for the Aero uh side um there's a whole lot of very low volume High mix parts that are Legacy parts that have been Troublesome to make over the years and additive can be can be close to a magic wand for that it's really there are a lot of opportunities there yeah it's probably a good segue um what what capabilities does starhagen have specifically um like in terms of the printer size or the Alloys that you have access to um so we have you know on the additive side we have two Velo sapphires um standard uh standard sapphires uh the one that was on the right side is running in Canal 625 and the one on the left is running aluminum f357 uh I believe to date we're the only uh shop that's running Novella with aluminum in it uh here in the US and so it's a lot of fun to work with I get to make some really cool Parts on it and they they look great and I love particularly um the part that I was just working on a few minutes ago before this call I would not be able to make on Another Printer but you know what I stuck it in here and I'm like I don't have to worry about my overhand angles here it's just gonna just drop it in and go so um in that respect it's a lot of fun to work with and you mentioned the inconel 625 I know a lot of customers are using the 718 but 625 has some interesting characteristics that make it uh kind of advantageous compared to 718 in some cases I would I would very much agree with that um so a lot of our uh space customers particularly um they prefer 625 because it's much more resistant uh to hydrogen uh prop uh hydrogen problems and uh the other thing is there's far less Heat Treating that you do for 625. I would say people typically use 625 more for ductility and corrosion resistance versus 718 it is a little bit stronger but it takes you know four heat treat Cycles to get to that strength and it's you know you're talking 27 hours of heat treating uh on a part so it does add substantial cost to it yeah and that's definitely something that should not be an afterthought when you're looking at it if you've got to look at your post processing your heat treating your Machining all of that it's got to be done up front um so these Alloys kind of give you access to maybe some different customers um to the degree that you can can you give us a couple success stories with customers um so we work with a local company corbid Technologies um and they uh do all kinds of really innovative solutions for um you know I've worked with them in the past life on warheads and missiles and other defense related systems uh earlier this year we made some missile fins for them that are in development for a new type of Deployable wing on a missile and that was really fun it used my entire build volume um so it was they were really fun to make uh I wish I could show you pictures of it but it's an itar part I can't show you yeah sorry um we you know another one like I said those uh those rocket at stage two rocket engine parts that we made for um space custom commercial space customer uh right when I started here those were a huge success and I'm very proud of them right now we're making some manifolds for a Navy submarine that is you wouldn't know it's a manifold to look at it because it's all lattice and it's very very complex but um it builds great and it's we're very optimistic that it's going to provide severe um Superior Mechanical properties over the Legacy system so I mean fins don't jump to the Forefront when I think about an additive part what is it about additive and defend how does how do those go together are you allowed to talk about that a little bit at a high level I would say in this particular case they were working on a new type of deployment for um what I could say is that so missiles frequently you see hanging off the wing of a plane have the fins in place and um you know they're fixed these were for a tube launch type design so they had to be Deployable so they had to retract and extend as they were fired okay yeah we have to have to be really vague in these conversations a lot of times now that's pretty awesome I I do I I know from some of the parts that we have been able to talk about in the past these rocket engines are just amazing like you're packing in so much now you've got injectors built in or conformal or not conformal um regenerative cooling uh built in and it's all printed in one go or what what have you seen in terms of the functionality that people are putting into these parts that maybe surprises you um boy you know so I a great example is I'm good friends with a number of folks over at SpaceX and have worked with them in the past and will probably be hopefully work working with them more now here at starhagen but um they are a really good example of building all that functionality into a part and thinking you know what can we do with this what you know what parts can we incorporate into this and uh reduce the uh the supply chain for it um the other one was it was a relativity space that just launched uh 85 percent uh additive rocket um that is that blew my mind um that they did um uh DED Direct Energy deposition on such a massive scale um it's it really blew me away but I mean I I love the Innovation and I love the design Freedom that we get um and working with so many diverse customers you know I get to learn from them too just from their designs I learned like oh hey that's a really neat application of a technique and I'm you know I can translate that into helping others you know with their designs as well to uh help them incorporate features that they previously wouldn't have thought of so we have um a kind of a question here maybe a lead for you um someone's asking I need aluminum frames for my solar inventions uh think about tracking high winds water loads would there be components in there that you think would would be additive and obviously you have traditional manufacturing Solutions as well so you'd probably be able to meet this this customer's requirement either way um I would think so and I um yeah and the gentleman or the is that sorry it's Charisse I think it is uh yes please reach out to me on LinkedIn and I'll be happy to help awesome um and there were some there's a question about the PLM systems uh can you expand on which systems you're referring to when you talk about digital files and configuration management um so the with regard to PLM systems I've used uh product Center and uh Siemens NX or Siemens uh well we use Siemens NX with the PLM uh bolt-ons uh some of the challenges with it are you know so design Engineers like to make different configurations they'll have tabular type uh tabular driven components so you know you have a whole family of different Dash numbers um it's real easy if you're not very meticulous about both your file naming convention but also your file control and uh how you work back from the end design files backwards towards your additive file it's very easy to uh slip up and basically get the wrong file and get the wrong configuration okay yeah that sounds complex um I I do I notice we're getting close to 30 minutes if you we probably have time for maybe one or two more questions from the audience um but it will ask some of uh I didn't want to ask one question what have you seen over the last 20 years that surprised you the most both in you didn't think the industry would do it but it did and maybe on the other side of that is um you know the industry really should have done something and and it still needs to do it um well I'll take your second one first uh I still feel that we don't have sufficient onboard in-situ monitoring um for defect detection uh there's a lot of people working on it and there's some good developments on it but I don't see a whole lot of production ready versions that are out there on many machines um I with The Velo system we've got I love the access to the sensors that I've got and the assure system and all that it's way better than anything I've worked with in the past so there's that um as far as what I've seen that I never would have thought about it's a tough call um codes and compliances or ASTM work I'm sorry uh you mentioned some of your work that you did on kind of getting um standardization in the industry yes we've uh We've made a lot of progress over the last 10 12 years I started with ASTM back in 2010 and helped create a number of the standards but um more ASTM or AMS standards are definitely desirable there's some really good ones that have been coming out by AMS recently particularly AMS 7000 series um the 7000 through 7003 for inconel I use those day in and day out um and 75-32 as well so those are great um you know frankly if I got to pick one thing for something I never would have seen predicted 20 years ago I would have said that relativity space rocket the 85 additive rocket I would not have uh I wouldn't I wouldn't have seen that coming yeah the whole Space Race in general is just amazing how quickly it's been moving forward and how closely it's working with additive and I don't think those are an accident that those are correlated the way they are um so kind of a a finishing topic but where do you think the industry is going to go in the next five to ten years what do you if you had to look into a crystal ball what what do you think we have coming down the pipeline well um I see a whole lot of evolution in drones you know the the whole situation in Ukraine has just seen you know necessity demands Innovation and um I can't speak to some of the innovations that I've seen that they're doing um or that some of our our customers are using to support them but it's incredibly impressive it's also frankly a little bit scary um what you know I think what will uh because I I do see drones being a a particular challenging area both in terms of military and just frankly civil aviation the danger that irresponsible use of it could do and frankly there's a whole lot of uh really good printer is like you know I've got one behind me it's uh it's a bamboo that you know I can make I could probably make almost an entire drone with that and um I know people who are doing exactly that so I see that as being one of the challenges but you know I see way more evolution in big parts and light weighted Parts um you know actually I see probable Automotive applications you know getting into the high volume components uh that you know frankly the the value proposition wasn't there a few years ago but I see us with these newer bigger systems with lots of lasers we are going to be able to really crank out Parts at a very high rate yeah I think uh and if you're interested in Velo 3DS experience in automotive we do have a 3D and 30 on that um and so uh we can put a link to that in the bottom but we are kind of closed up on time I do want to thank our audience for attending uh you've been great I love the questions um in the comments Matt you have a lot of fans out there a lot of people are saying hi and hello so um you know make sure to give them a thumbs up when you can uh and Matt thank you for being on the show um I I know we had some topics we weren't able to get to but I love deep diving into some of your experience and your backgrounds I love bouncing off ideas uh to see what your perspective is uh fantastic resource so thank you very much for being on the show thank you this is this is a lot of fun uh I'll love to do it again or uh talk offline without anybody who's anybody who's interested or has questions you know that's what I love about our industry is we're very small and tight-knit and you know my competitors call me for help I call them for help and we all help each other out um you know we're competitors but we all want to see the Technologies succeed and um you know I love solving problems for customers so you know it's uh that's really why I do what I do awesome well thank you Matt and that's a wrap for our show today thanks a lot Mike
2023-08-10 14:19